Our Surface Finishing Capabilities
Use HLH as your one-stop solution for both manufacturing and surface finishing of your custom parts, reducing the risk of production. Here is a list of standard surface finishes. For custom surface finishes such as laser cutting or hard anodizing, please contact: info@hlhmold.com
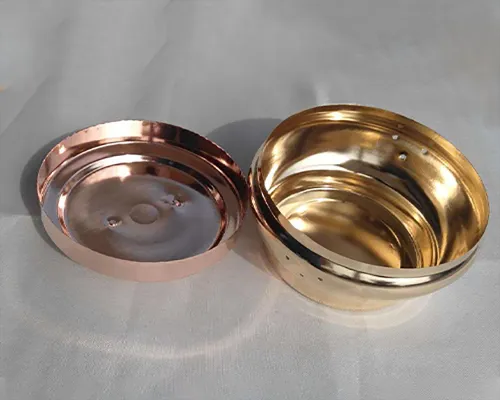
POLISHING
Polishing - The exquisite finishing process that gives materials an ultra-smooth surface

Definition:
friction or chemical action, resulting in a smooth, highly glossy or special textured finish.

Characteristics:
Enhanced finish: Surface roughness can reach Ra 0.01μm (mirror finish level)
Enhanced functionality: Reduces friction resistance, improves sealing performance, and enhances corrosion resistance
Aesthetic value: Customizable visual effects such as metallic luster / matte or frosted finish
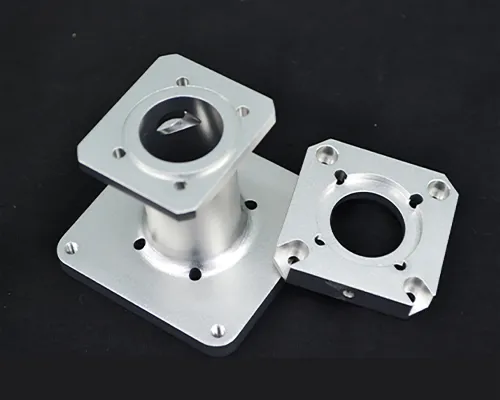
ANODIZING
Anodizing - An electrochemical process used to enhance the surface of metals

Definition:
Anodizing is a process that forms a dense oxide film on the surface of metals such as aluminum, titanium, and magnesium through an electrolytic reaction:

Characteristics:
High hardness: The hardness of the oxide film can reach HV300-500, significantly enhancing the surface wear resistance.
Corrosion resistance: After sealing treatment, it can withstand salt spray tests for 500-1000 hours.
Insulation performance: The resistance of the oxide film reaches 10⁹ - 10¹² Ω·cm.
Decorativeness: Electrolytic coloring can be used to obtain 20+ standard color schemes.
Adhesion: The oxide film is metallurgically bonded to the substrate and never peels off.
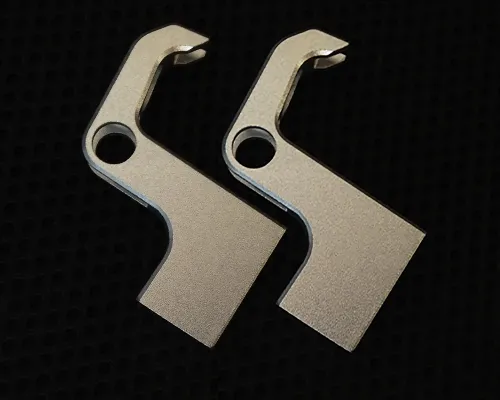
SAND BLASTING
Sand Blasting - The "beauty polishing technology" for metal surface treatment

Definition:
A physical processing technique that achieves cleaning, roughening or matte finish effects by subjecting the metal surface to high-speed impact with abrasive materials (such as quartz sand/glass beads/steel balls, etc.).

Characteristics:
Remove contaminants: It can remove the oxide layer, oil stains, rust, old coatings, etc. from the surface.
Efficient Handling: Suitable for complex shapes or inaccessible areas (such as crevices, grooves)
Enhanced Adhesion: By creating micro-roughness structures, it enhances the adhesion of coatings (such as paint, coating).
Uniformity: Capable of controlling the roughness (such as at the Sa2.5 standard), suitable for subsequent process requirements.
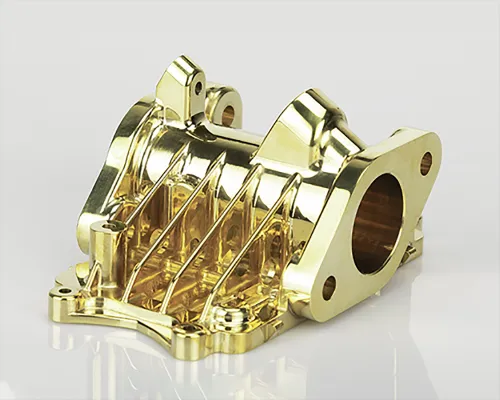
ELECTROLYTIC POLISHING
Electrolytic Polishing - A process that precisely polishes the surface of metals using electrochemical methods.

Definition:
Electrolytic polishing is a technique that removes microscopic protrusions on the metal surface through electrochemical dissolution, resulting in an extremely smooth surface:

Characteristics:
Microscopic leveling: By selectively dissolving the raised parts on the surface, the roughness is reduced (reaching Ra 0.1 μm or below), achieving a mirror-like effect.
Luster enhancement: Eliminating mechanical processing marks (such as scratches, burrs), enhancing the reflectivity of the metal.
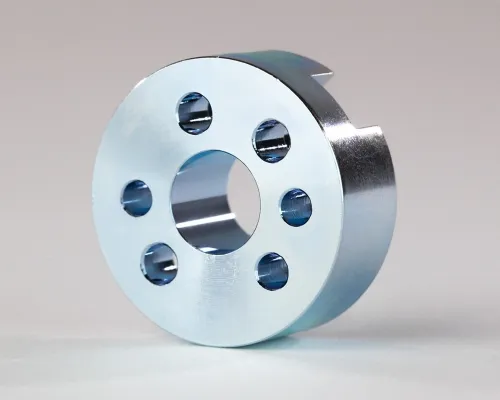
GALVANIZING
Galvanizing - The Classic Process for Preventing Metal Corrosion

Definition:
Galvanizing is a technique that involves covering the surface of steel with a zinc layer (5-150 μm) to prevent exposure to corrosive media.

Characteristics:
Excellent anti-corrosion performance, sustainability
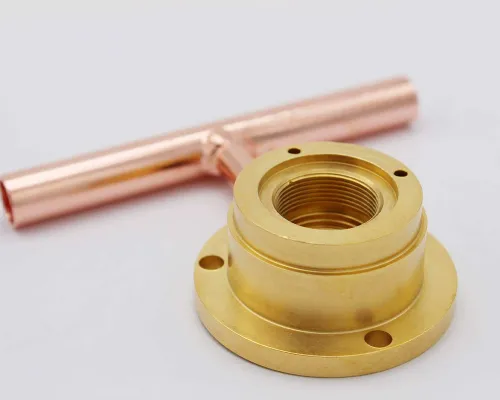
PASSIVATION
Passivation - Chemical enhancement technology for metal corrosion prevention

Definition:
Passivation is a process that forms a dense oxide film on the metal surface through chemical or electrochemical methods to enhance corrosion resistance.

Characteristics:
Chemical stability: The passivation film is not easily dissolved in most acids, bases, and salt solutions.
Density: The film layer is extremely thin (at the nanometer level) and has no pores, effectively preventing corrosive media from penetrating.
Self-repairing property: After local damage, a new passivation film can be re-formed under oxidative conditions.
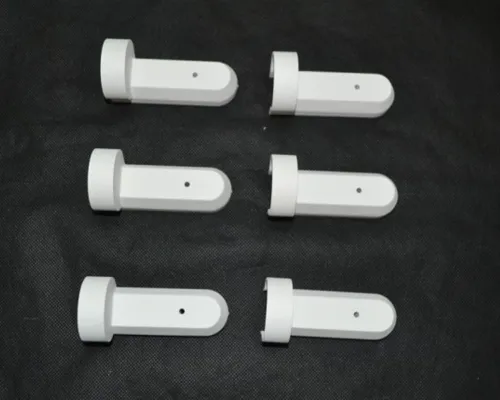
POWDER COATING
Powder Coating - An Environmentally Friendly and Highly Efficient Surface Coating Technology

Definition:
Powder coating is a technology that uses electrostatic adsorption to spray solid powder onto the surface of a metal, and then undergoes high-temperature curing (typically at 180-200°C) to form a dense coating.

Characteristics:
Environmental friendliness, economy, insulation, wear resistance, impact resistance
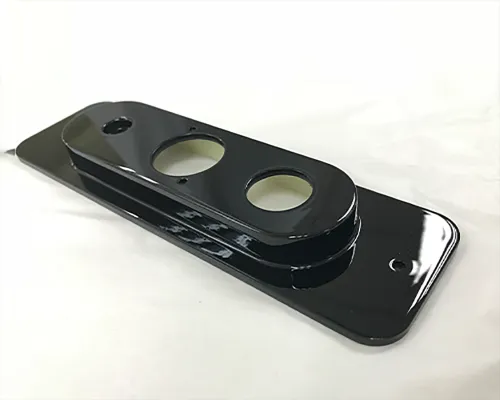
PAINTING
Post-processing (Spray Painting) — The Sublimation Stage of Artistic Creation

Definition:
"Post-processing (Spray Painting) — The Sublimation Stage of Artistic Creation""Spray painting is a surface treatment technology that uses spraying equipment to evenly coat (oil-based/water-based) paint onto workpiece surfaces, forming protective or decorative layers. It is widely applied to materials such as plastics, metals, and wood."

Characteristics:
Post-processing (painting) - The elevated stagHigh Decorative Quality
Achieves diverse visual effects including mirror gloss, matte finishes, metallic textures, and gradient colors.
Superior Protective Performance
Forms a dense coating resistant to corrosion, UV rays, and scratches (salt spray testing exceeds 500 hours).
Wide Material Compatibility
Applicable to various substrates such as plastics (ABS/PC/PP), metals, and fiberglass.