Design Guides
Fused Deposition Modeling (FDM) systems and related technologies are the most accessible and widely used form of 3D printing. FDM machines build parts layer-by-layer from the bottom up by heating and extruding thermoplastic filament. The production-grade thermoplastic material used is suitable for detailed functional prototypes, durable manufacturing tools & low-volume manufacturing parts.Different industries require different solutions to maximize the efficiency of their objective. FDM 3D printing technology builds durable and functional prototypes that can withstand rigorous testing.
FDM Design Guides
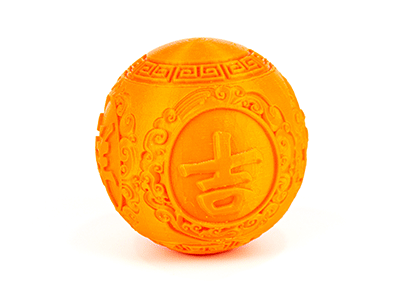
Tolerances: +/- 0.3mm is standard.
Walls: FDM can manage very thin walls but QSY do not recommend anything under 0.8 – 1mm.
Overhangs: Not a problem for SLA due to the supports. Unsupported overhangs will warp.
Holes & Slots: We recommend a minimum of 0.5mm but the larger the better especially as wall thickness or depth increases.
Text & Engraved Details: Are at risk of closing up if not designed with 0.5mm > minimum height.
Pins & Embossed Features: Pins ≥ 0.8mm but even then risk breaking. Embossed features ≥ 0.3mm.
Mating Parts: Minimum 0.5mm gap between axel and bore or other moving parts.
