3D Printing Filaments: Your Path to Prototype Perfection!
Navigation
- Introduction
- Application Requirements
- Compare Filament Properties
- Take Material Costs Into Account
- Review Print Processing Factor
- Recommended Materials for Key Applications
- Don’t Overlook Composite Materials
Filament Type | Mechanical Strength | Heat Resistance | Detail Accuracy | Aesthetic Finish | Recommended Use |
---|---|---|---|---|---|
PLA | Low | Low | High | Glossy | Conceptual Models |
ABS | High | Moderate | Variable | Glossy when finished | Durable Parts |
PETG | Good | Higher than PLA | Moderate | Glossy | Balanced Prototypes |
Nylon | High | Excellent | Tricky | Needs finishing | Durable, High Temp Parts |
TPU | Very Durable | Moderate | Variable | Rubbery | Flexible Parts |
PC | Very High | Very High | Challenging | Smooth with processing | High Stress, Temp Parts |
PP | Moderate | Good | Difficult | Matte | Flexible, Durable Parts |
Introduction
When you’re dealing with 3D printing prototypes, picking the perfect filament is key to get the properties, precision, strength, and look you want for your printed piece. With so many thermoplastics to choose from for fused deposition modeling (FDM) or fused filament fabrication (FFF), how do you figure out the best material for your project? This piece gives you some handy tips on selecting filaments, considering things like how well they perform mechanically, how stable they are dimensionally, how they resist temperature, how they look, and more. For more in-depth information, check out this blog post on how 3D Printing Prototypes are Driving Business Benefits.
Application Requirements
First and foremost, you need to consider the functional requirements of the prototype. What will the printed part be used for? Does it need to withstand mechanical loads or environmental exposure? Highlighting these specifics will help narrow down suitable filament options. For example, a conceptual model for form and fit testing would have less stringent requirements than a functional prototype meant for engineering evaluations under real-world conditions.
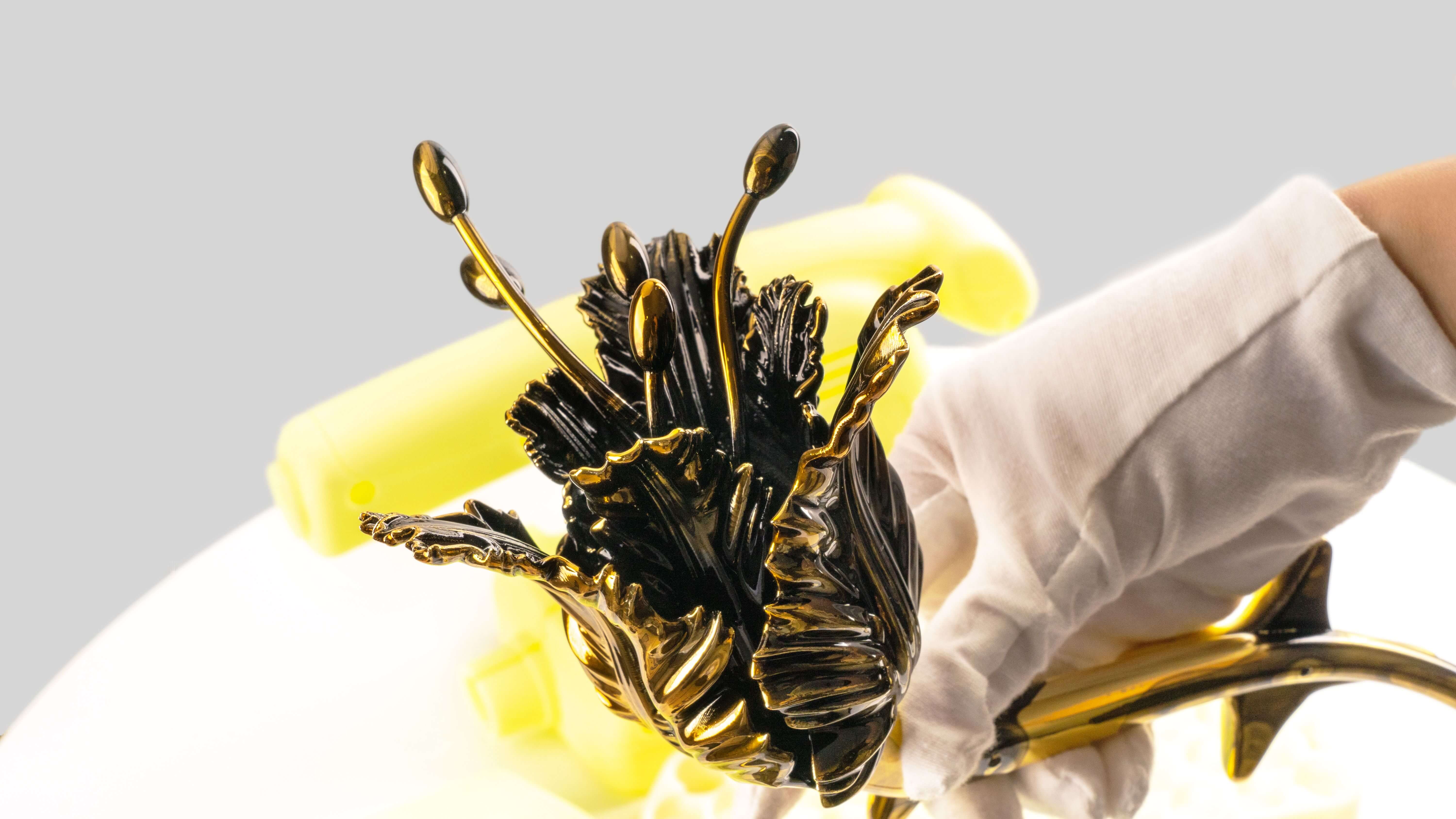
Compare Filament Properties
Once you have a clear understanding of the functional requirements and intended use environment for your 3D printed prototype, the next step is to analyze and compare the relevant material properties of different filament options. This in-depth evaluation across key performance criteria will reveal the strengths and limitations of each candidate plastic and empower you to select the optimal match for your application.
Mechanical Properties
Tensile and flexural metrics indicate the inherent strength of the material when under tension or bending loads. A higher tensile modulus and flexural modulus suggest suitability for parts that must withstand higher stresses without permanent deformation. For movable components with snap fits, flexible materials that allow repeated cycles without cracking are preferable.
Specifically, hardy engineering materials like ABS and nylon usually offer the best strength and rigidity for functional prototypes that are meant for physical testing. On the other hand, flexible thermoplastic polyurethanes (TPU) provide rubber-like flexibility for connecting joints and living hinges. You should compare the elongation at break values to get a sense of relative ductility. Basically, you need to look at filament mechanical data in relation to the forces and movements your prototype will realistically face. If you’re looking for professional help with this, consider using an SLS 3D printing service.
Thermal Properties
Look at the heat deflection temperature and melting point. Materials with thermal stability well above operating temperatures are less prone to undesirable creep or distortion when prototypes mimic real-world environments. Compare upper-temperature limits to any heating processes also used in post-processing, like vapor smoothing, which exposes prints to solvent vapors at elevated temps. High-temperature Nylons are suitable for hot fluid testing; PETG can handle occasional heat spikes, while PLA has the lowest working temps.
Dimensional Accuracy
For prototypes with press-fit assemblies or functional tolerances, the tendency for the print material to shrink or expand upon cooling over time affects achieved part accuracy. ABS is known for significant shrinkage versus other widely printed plastics. Analyzing filament shrink rates helps identify better options for dimension-critical prototypes like jigs, fixtures, and housings needing precise fittings.
Aesthetics
Surface smoothness impacts perceived quality and paintability for prototypes where aesthetics matter, like external casings and consumer products. PETG offers a glass-like surface that takes paint evenly compared to the layers left by ABS. Knowing the ease of achieving a smooth, professional-looking finish via vapor polishing or coating compatibility steers material decisions when appearance is on your priority list for a concept model.
Evaluating this range of filament metrics against requirements makes the capabilities of each plastic evident, bringing you one step closer to the right material choice. Leverage supplier data sheets don’t hesitate to request physical samples, and probe technical contacts with questions to fully grasp how shortlisted materials relate to expected prototype performance.
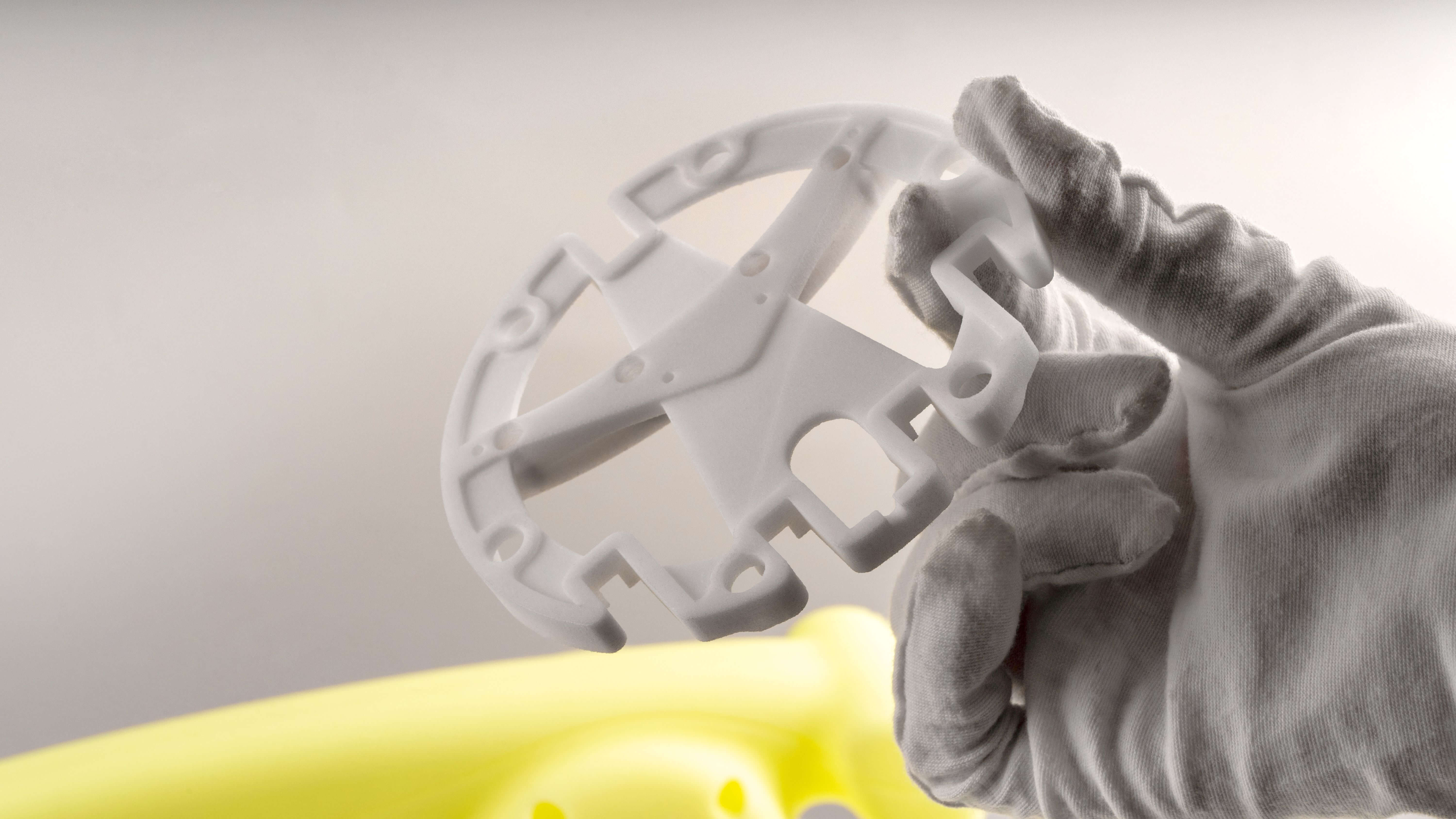
Take Material Costs Into Account
Filament choice also impacts overall prototype expenses in terms of material costs. While exotic-filled nylons and PC blends have outstanding properties, common plastics like ABS and PLA can offer the best value for cost-sensitive concept modeling and early testing stages. It’s prudent to first evaluate whether more affordable materials can meet design needs before opting for pricier options. If they fall short, you can then justify the additional costs for engineered grades that fulfill all requirements.
Review Print Processing Factor
Ideally, the filament type should also align with your printing set-up, workflow, and post-processing needs:
- Nozzle temperatures – Verify that the polymer prints at nozzle temperatures are compatible with your printer hardware. Temperatures above 250°C typically need specialized hot ends.
- Bed adhesion – Filaments require specific bed coatings/adhesives or surface treatments to stick while printing. ABS notoriously struggles on bare glass, for example.
- Warping behavior – Some materials like ABS are prone to warping due to internal stresses, so enclosed printers or substrate heating may be necessary.
- Ease of supporting removal – Overhangs and complex geometries need dissolvable supports for suitable materials. Breakaway supports work better for brittle plastics.
Recommended Materials for Key Applications
With an awareness of key material characteristics and print processing considerations, we can now examine typical applications for FDM prototyping and review some of the best filament options suited for each use case.
Concept Models
PLA and PETG are great introductory materials for early-stage concept models focused on form, fit, and basic function. PLA is the most widely printed plastic, given its ease of use and affordable price point. Warping is minimal, allowing large flat prints. While mechanically weaker than other plastics, PLA concept models handle basic testing and can serve as masters for urethane casting. PETG steps up when improved strength, flexibility, smoother finish, and higher temp resistance (up to 70-80°C) are preferred.
Functional Prototypes
ABS and PC target working prototypes meant for engineering evaluations simulating real-world conditions. Strong, versatile ABS allows functional testing under various temperatures, and smoothing with acetone vapor enables glossy models that mimic production materials. PC offers even higher rigidity and heat resistance up to 115°C while maintaining ductility. Consider PC when dimensional stability under temperature matters most. Both satisfy advanced requirements, albeit at higher costs.
End-Use Parts and Fixtures
Glass or carbon-reinforced nylons bridge the gap when a prototype transitions onwards into a production end-use part, rugged, functional fixture, or high-cycle test rig. By embedding structural reinforcements, engineers amplify the native durability of nylons. For example, Onyx (chopped carbon-filled nylon) approaches aluminum properties but prints reliably via FDM. Depending on loads, higher-filled versions may suit demanding applications. Conductive carbon and ESD-safe nylons also suit electronic fixtures.
Flexible, Moving Components
TPU, flexible PLA, and thermoplastic elastomers (TPE) fulfill rubber-like compliance for functional components needing realistic flexing, expansions, or living hinges like tubes, seals, and mechanisms with snap joints. The exceptional abrasion resistance and durability of quality TPUs outweigh their steeper pricing. FDM processing can struggle with some highly flexible materials, so check printer compatibility.
Food Contact Applications
Polypropylene (PP) and PETG stand out for food contact prototypes thanks to inertness meeting FDA and EU regulations under proper processing protocols. Choose PP for fattier and hotter foods, given its exceptional chemical resistance and higher melting point. PETG suits water bottles and cooler containers. Approvals mainly apply once prints are properly prepared via annealing, curing, and smoothing methods to avoid porous surfaces.
Evaluating candidate materials in relation to typical prototyping applications provides a practical perspective into matching filaments with their highest utility. Blend background knowledge of material strengths with specific functional priorities and process considerations to ultimately land on a resin that ticks all the boxes for your project. The most informed selections yield the parts best equipped to meet expectations.
Don’t Overlook Composite Materials
With composite filaments, polymers are blended with reinforcements like wood, metal, or carbon fibers to attain enhanced properties compared to base resins. Common combinations include PLA or ABS with chopped carbon fiber or graphene. These composites bridge the performance gap between unfilled plastics and high-cost engineered filaments. Wood and metal fiber blends also enable unique aesthetics. Just be aware that print settings may need tweaking for optimal composite part quality.
Final Words
In summary, carefully deliberating application requirements, comparing material characteristics, evaluating processing factors, and relating needs to recommended filaments leads to the best-informed decisions on prototypes. Leverage filament supplier data, ask material suppliers questions, and don’t hesitate to request samples to physically trial candidates. With some diligence upfront, you’ll choose the optimal match and avoid wasted time and materials from poor choices. The extra effort spent on material selection determines whether your printed prototype fully meets expectations and functionality needs.