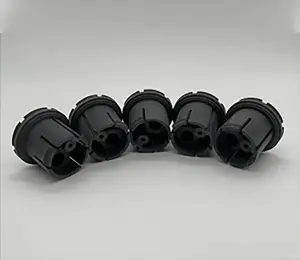
POM (DELRIN/ACETAL)
POM (Polyoxymethylene) is a high-performance engineering plastic known for its outstanding mechanical strength, rigidity, wear resistance, and chemical resistance.

Features:
High Rigidity & Low Friction: Ideal for parts requiring high wear resistance and self-lubrication.
Fatigue Resistance: Resists deformation under repeated stress, making it suitable for dynamic components.
Chemical Resistance: Performs well against oils, solvents, and weak acids/bases but is not resistant to strong acids or alkalis.
Low Water Absorption: Offers excellent dimensional stability, making it suitable for precision parts.
Ease of Processing: Can be manufactured via injection molding, extrusion, or CNC machining.

CNC Applications:
Mechanical Components: Gears, cams, bearings, bushings.
Industrial Parts: Valves, pump components, clamps, guide rails.
Electronic Devices: Insulating parts, connectors, precision structural components.
Medical Equipment: Surgical instrument parts, testing device components.
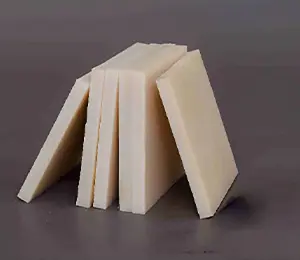
NYLON
Nylon is a synthetic polymer (polyamide).

Features:
High Strength & Wear Resistance: Stronger than many plastics, suitable for withstanding mechanical stress.
Lightweight: Low density, often used to replace metals for weight reduction.
Chemical Resistance: Resistant to oils, fuels, and certain solvents, but may be corroded by strong acids/bases.
Self-Lubricating: Low friction coefficient, ideal for moving parts like gears and bearings.
Temperature Range: Typically withstands -40°C to 120°C (some modified grades can endure higher temperatures).

Applications of CNC Machined Nylon:
Industrial Components: Gears, bearings, sliders, bushings.
Automotive: Under-the-hood parts, sensor mounts.
Aerospace: Lightweight structural components, drone parts.
Medical: Surgical tool prototypes, non-implantable devices.
Electronics: Insulating housings, connectors.
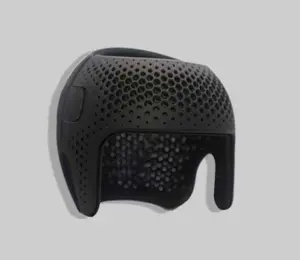
ABS
ABS (Acrylonitrile Butadiene Styrene) is a thermoplastic polymer known for its excellent combination of properties.

Features:
Mechanical Properties: High strength, good toughness, and strong impact resistance.
Chemical Resistance: Resistant to acids, alkalis, and oils, but soluble in ketones and esters (e.g., acetone).
Processability: Easy to process via injection molding, extrusion, 3D printing (e.g., FDM technology), and CNC machining.
Other Features: Good electrical insulation, surface can be electroplated or painted, but poor weather resistance (prone to UV degradation).

Applications:
Automotive parts (e.g., dashboards), electronic enclosures, toys (e.g., LEGO bricks), household items, etc.
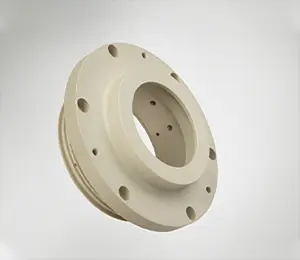
PEEK
PEEK (Polyether Ether Ketone) is a high-performance thermoplastic specialty engineering plastic.

Features:
High-temperature resistance: Long-term service temperature up to 250°C, short-term tolerance exceeding 300°C.
High strength & rigidity: Mechanical properties close to metals, with excellent creep and fatigue resistance.
Chemical stability: Resistant to acids, alkalis, organic solvents, fuels, and other corrosive substances.
Wear resistance & self-lubrication: Low friction coefficient, suitable for moving parts like bearings and gears.
Insulation properties: Outstanding electrical insulation performance, used in electronics and electrical applications.
Biocompatibility: Used in medical implants (e.g., spinal fusion devices).

Applications:
Aerospace components, automotive fuel systems, semiconductor equipment, medical implants, petrochemical seals, etc.
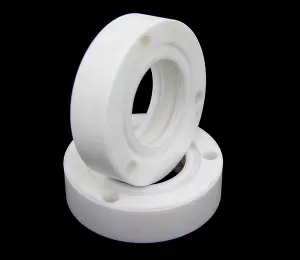
PTFE (TEFLON)
PTFE (Polytetrafluoroethylene) is a high-performance fluoropolymer.

Features:
Chemical inertness: Resistant to strong acids, alkalis, and nearly all organic solvents.
Temperature resistance: Wide operating temperature range (-200°C to +260°C).
Low coefficient of friction: Extremely smooth surface with a friction coefficient close to that of ice.
Insulation properties: Excellent electrical insulation performance.
Non-stick: Almost no adhesion to any substance (commonly used in non-stick cookware coatings).
Mechanical properties: Soft and wear-resistant, but with low rigidity and prone to creep.

Applications:
Seals, insulating components, medical devices, aerospace.
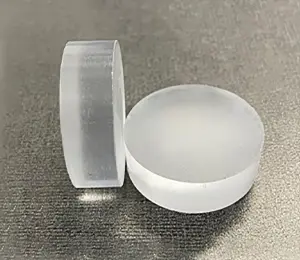
POLYCARBONATE
Polycarbonate is a high-performance thermoplastic known for its excellent mechanical properties, transparency, and heat resistance.

Features:
High Impact Resistance: 250 times stronger than glass and 30 times stronger than acrylic.
Transparency: Light transmittance comparable to glass (up to 90%), available in transparent, translucent, or opaque variants.
Heat Resistance: Wide operating temperature range (-40°C to 120°C), with short-term tolerance for higher temperatures.
Lightweight: Low density (~1.2 g/cm³), significantly lighter than glass.
Electrical Insulation: Suitable for electronic components.
Weather Resistance: UV-resistant (some variants feature UV-protective coatings).

Common Applications:
Safety goggles, bulletproof glass, automotive lamp covers, electronic housings, medical devices, transparent protective shields, etc.
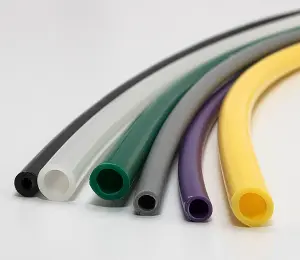
POLYETHYLENE
Polyethylene is a thermoplastic polymer formed by the polymerization of ethylene monomers.

Features:
Ease of Processing: Soft PE (e.g., LDPE) has low cutting resistance and causes minimal tool wear.
Non-Stick Properties: Compared to materials like PVC, chips are less likely to adhere to cutting tools.
Dimensional Stability: Extremely low moisture absorption (<0.01%), resulting in minimal deformation after processing.

Applications:
Industrial components, medical devices, food packaging, automotive parts, etc.
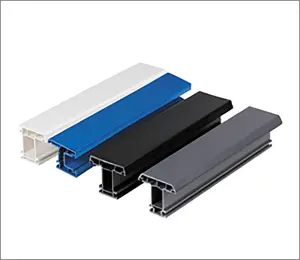
PVC
PVC (Polyvinyl Chloride) is a widely used thermoplastic polymer synthesized from the polymerization of vinyl chloride monomers. Depending on additives, it can be categorized into rigid PVC (e.g., pipes) and flexible PVC (e.g., cable sheathing).

Features:
Corrosion Resistance: Resistant to chemicals such as acids, alkalis, and oils.
Insulation: Excellent electrical insulation, commonly used in wires and cables.
Flame Retardancy: Self-extinguishing when flame retardants are added.
Mechanical Strength: Rigid PVC offers high strength, while flexible PVC is highly pliable.
Low Cost: Affordable raw materials and easy processing.

Applications:
Construction pipes, window/door profiles, medical devices, packaging films, flooring, etc.

PMMA (ACRYLIC)
PMMA (Polymethyl Methacrylate), commonly known as acrylic or organic glass, is a transparent thermoplastic polymer.

Features:
Optical Performance: Light transmittance up to 92%, superior to ordinary glass, with UV resistance.
Mechanical Properties: High hardness and scratch resistance, but relatively brittle and lower impact resistance compared to polycarbonate (PC).
Chemical Stability: Resistant to weak acids and alkalis but soluble in organic solvents such as acetone and chloroform.
Processability: Easy to cut, engrave, heat-bend, and injection mold.

Applications:
Advertising signage, optical lenses, display stands, medical devices, automotive lamp covers, etc.

PET
Polyethylene Terephthalate (PET)

Features:
A thermoplastic polyester that is transparent, lightweight, high-strength, and chemically resistant (resistant to acids, oils, and alcohols).
Melting point around 250°C, operating temperature range from -40°C to 120°C.
Excellent gas/moisture barrier properties, commonly used in food packaging (e.g., beverage bottles).

Applications:
Packaging (bottles, films), fibers (clothing), electronic components (insulating materials), 3D printing, etc.

POLYPROPYLENE (PP)
Polypropylene (PP) is a thermoplastic polymer produced by the polymerization of propylene monomers and belongs to the polyolefin family.

Features:
Lightweight: Low density (0.9–0.91 g/cm³), lighter than many plastics.
Chemical Resistance: Excellent resistance to acids, alkalis, and solvents (except strong oxidizers).
Heat Resistance: Melting point around 160–170°C, can withstand short-term exposure to 120°C, but becomes brittle at low temperatures.
Mechanical Properties: Good rigidity, though impact resistance can be improved through copolymer modification.
Electrical Insulation: Excellent high-frequency insulation properties, making it suitable for electronic components.

Applications:
Industrial components, medical devices, electronics, packaging molds, automotive parts.

G-10
G-10 is a high-performance glass fiber-reinforced epoxy resin composite material, classified as an industrial-grade laminate.

Features:
High strength and rigidity, with excellent mechanical properties.
Extremely low moisture absorption, resistant to humidity and chemical corrosion (e.g., acids, alkalis, solvents).
Outstanding electrical insulation, commonly used in electronics.
Wide operating temperature range (-50°C to +150°C).

Applications:
Circuit board substrates, insulating components, aerospace parts.
Knife handles, high-load structural components, etc.
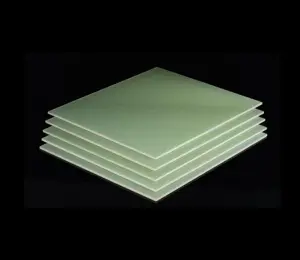
FR4
FR4 is a flame-retardant substrate material composed of fiberglass cloth and epoxy resin composites. It is an electronic-grade insulating material that meets the UL94 V-0 fire safety standard.

Features:
Electrical Properties: High insulation, low dielectric constant, suitable for high-frequency circuits.
Mechanical Properties: High strength and rigidity, but relatively brittle (prone to cracking).
Heat Resistance: Operating temperature typically ranges from 130°C to 140°C (higher TG value indicates better heat resistance).
Flame Retardancy: UL-certified, self-extinguishing.
Machinability: Can be drilled and milled, but abrasive to cutting tools (due to fiberglass content).

Applications:
PCB circuit boards (rigid boards), insulating brackets, electrical equipment enclosures, high-frequency electronic devices (e.g., antenna substrates).

ALUMINUM
Aluminum and its alloys (such as 6061, 7075, 5052, etc.) are among the most commonly used metals in CNC machining.

Features:
Lightweight yet strong: Low density (~2.7 g/cm³), but some alloys (e.g., 7075) have strength comparable to steel.
Excellent machinability: Low hardness (HB50-120), minimal cutting resistance, reduced tool wear, and suitable for high-speed machining.
Good thermal & electrical conductivity: Ideal for heat dissipation components or electronic parts.
Corrosion resistance: Forms a natural oxide layer, with further protection possible through anodizing.
Versatile surface treatments: Supports anodizing, sandblasting, electroplating, and other processes.

Applications:
Aerospace, automotive industry, electronics, industrial machinery, consumer products.

STAINLESS STEEL
Stainless steel is a corrosion-resistant and high-temperature-resistant alloy steel. Its primary components are iron (Fe) and chromium (Cr) (≥10.5%), and it may also contain elements such as nickel (Ni), molybdenum (Mo), and manganese (Mn).

Features:
Work Hardening: Stainless steel tends to harden during machining, accelerating tool wear (especially austenitic steels).
Gumming Tendency: Chips easily adhere to the cutting tool, affecting surface finish. Sharp edges and coated tools are recommended.
Poor Thermal Conductivity: Heat concentrates at the tool-workpiece interface, requiring enhanced cooling (e.g., using emulsion or high-pressure air cooling).
High Toughness: Chip breaking is difficult; optimized cutting parameters (e.g., feed rate, spindle speed) or chip-breaking groove tools are necessary.

Applications:
Medical equipment, aerospace, automotive industry, food machinery, industrial components.

MILD STEEL
Definition: Mild steel, also known as "low-carbon steel," is a soft type of steel with a carbon content ≤0.25%. It exhibits good plasticity and weldability.

Features:
Easy to machine, low cost, excellent weldability, high toughness.

Applications:
Structural components, industrial parts, mold prototypes, everyday products.
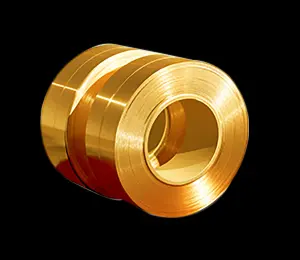
BRASS
Brass is an alloy of copper (Cu) and zinc (Zn), which may contain small amounts of other elements (such as lead, aluminum, or silicon) to enhance specific properties.

Features:
Easy chip-breaking, low friction coefficient, fast heat dissipation

Applications:
Precision components, piping systems, decorative fittings, industrial parts

COPPER
Copper is an important non-ferrous metal, featuring excellent electrical conductivity, thermal conductivity and corrosion resistance. It is widely used in the fields of electronics, construction, and industrial manufacturing.

Features:
Electrical/Thermal Conductivity: Pure copper has the second highest electrical conductivity after silver, making it widely used in the electronics and power industries.
Corrosion Resistance: Strong oxidation resistance, suitable for humid or chemical environments.
Ductility: Easily processed into complex shapes (e.g., wires, thin sheets).
Antimicrobial Properties: Commonly used in medical and food equipment.

Applications:
Electronics industry, industrial components, art and architecture, aerospace.
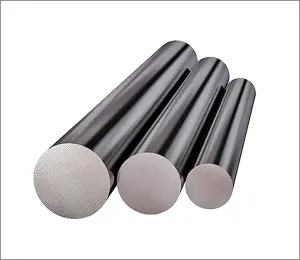
ALLOY STEEL
Alloy steel is a type of steel that is enhanced by adding other alloying elements (such as chromium, nickel, molybdenum, vanadium, manganese, etc.) to carbon steel to improve its mechanical properties, corrosion resistance, hardness, or heat resistance.

Features:
High strength, wear resistance, and high-temperature resistance.
Performance can be adjusted through heat treatment (quenching, tempering).

Applications:
Automotive industry, aerospace, mold manufacturing, toolmaking.

TOOL STEEL
Tool steel is a category of alloy steel specifically designed for manufacturing high-hardness, high-wear-resistance tools such as cutting tools, molds, and measuring instruments. It is characterized by a high carbon content (typically 0.5%–1.5%) and the addition of alloying elements such as tungsten (W), molybdenum (Mo), chromium (Cr), and vanadium (V) to enhance hardness, heat resistance, and wear resistance.

Features:
High Hardness: After heat treatment, hardness can reach HRC 60+, providing excellent wear resistance but making machining difficult.
Heat Resistance: Retains hardness at high temperatures (especially high-speed steel).
Low Thermal Conductivity: Prone to heat buildup, requiring controlled cutting temperatures.
Toughness Requirements: Some tool steels need to balance hardness with impact resistance (e.g., hot-work mold steel).

Applications:
Cutting tools, mold manufacturing, precision components, broaches, gauges, etc.
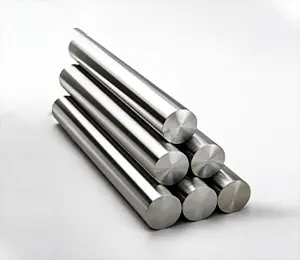
TITANIUM
Titanium is a lightweight, high-strength, and corrosion-resistant metallic material widely used in aerospace, medical, chemical engineering, sports equipment, and other fields.

CNC Machining Characteristics of Titanium
Rapid tool wear: Titanium's high strength and chemical reactivity easily lead to tool chipping and built-up edge.
Concentrated cutting heat: Poor thermal conductivity causes heat to accumulate in the tool-workpiece contact zone, requiring intensive cooling.
Risk of elastic deformation: Low elastic modulus results in workpiece vibration during cutting, affecting precision.
Tendency to adhere to tools: Titanium chips easily stick to cutting tools, necessitating optimized cutting parameters (e.g., high feed rate, low spindle speed).

Applications:
Aerospace, medical field, military/shipbuilding, high-end industrial

INCONEL
Inconel is a general term for nickel-based superalloys, composed of elements such as nickel (Ni), chromium (Cr), molybdenum (Mo), and iron (Fe). It exhibits properties like high-temperature resistance, corrosion resistance, and high strength, making it widely used in aerospace, chemical processing, energy, military, and other industries.

CNC Machining Characteristics (Inconel)
High Hardness & Work Hardening: The material hardens during cutting, leading to rapid tool wear.
Low Thermal Conductivity: Cutting heat dissipates poorly, causing tool overheating.
High Adhesion: Chips tend to stick to the tool, affecting surface finish.
High Cutting Forces: Requires rigid machinery and high-power spindles.

Applications:
Aero-engine components, petrochemical equipment, medical and nuclear industry parts.
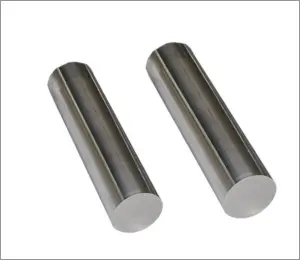
INVAR
Invar (also known as FeNi36 or invar alloy) is a nickel-iron alloy, typically composed of approximately 36% nickel with the remainder being iron. Its most notable characteristic is its extremely low coefficient of thermal expansion (close to zero at room temperature), meaning it exhibits almost no dimensional changes under temperature variations.

Features:
High Precision: Capable of achieving micrometer-level accuracy (±0.001 mm).
Automation: Reduces manual intervention and improves consistency.
Flexibility: Enables rapid task switching through program modifications.
Complex Machining Capability: Supports multi-axis coordination (e.g., 5-axis CNC machining for complex surfaces).
Efficiency & Repeatability: Suitable for medium to large-scale production.

Typical Applications:
Precision measurement equipment
Semiconductor manufacturing devices