4. Drying and Storage
The mold should be thoroughly dried in a cool environment (24-48 hours) to prevent mold growth due to moisture. For long-term storage, it is recommended to use a sealed bag and add desiccant, and keep it away from ultraviolet rays to avoid aging.
5. Performance Testing
Before the first use, a mold test is required to check the dimensional accuracy and demolding effect. Record the shrinkage rate and detail reproduction rate to provide data for subsequent process adjustments.
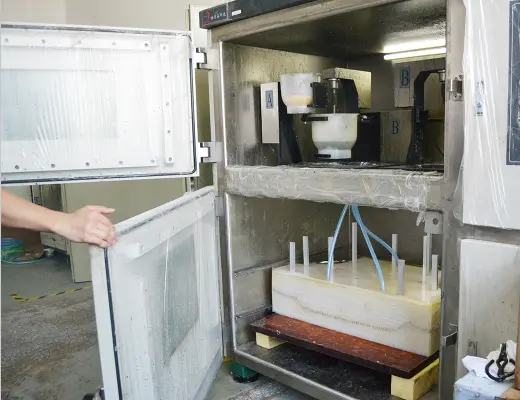

1:1 detail replication: Precisely recreates 0.1mm textures and complex structures

Diverse materials: 200+ types of engineering resins (hardness Shore A30-D90)

No minimum order quantity: Can be made individually, delivered within 3-5 days

No air bubbles in vacuum: Surface finish Ra1.6μm (optional mirror finish/ matte finish)