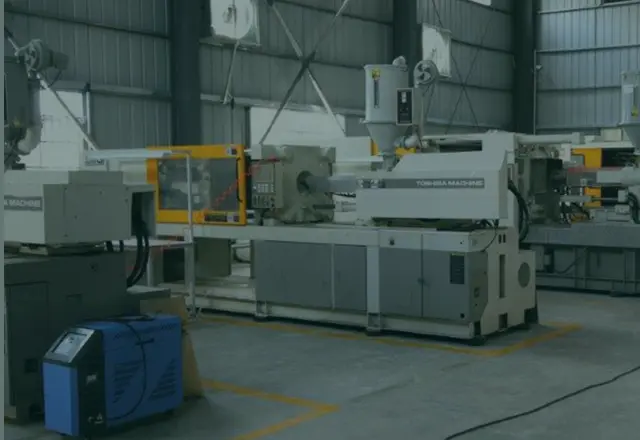
HOW MODERN PLASTIC
INJECTION
MOLDING WORKS
Injection molds are sophisticated tool systems used in modern manufacturing to achieve mass production of plastic products. Their working principle integrates cutting-edge technologies from mechanical engineering and materials science. The mold is composed of a high-precision cavity and core through which a closed space is formed. It remains tightly closed under the locking force of hundreds of tons applied by the injection molding machine's closing system. Melted plastic at a high temperature of 1500-3000 bar is injected into the mold cavity under the injection pressure, and the carefully designed flow channel system ensures uniform filling of each detail. The integrated temperature control system inside the mold precisely regulates the working temperature of 20-120℃, combined with the conformal cooling water channels to achieve a rapid and uniform curing process. The ejection mechanism removes the molded product without damage through a push rod or pneumatic device at the moment of mold opening. The entire cycle is completed within 15-300 seconds, with a repeatability accuracy of ±0.02mm. Modern intelligent molds are also equipped with pressure sensors and IoT modules, which monitor molding parameters in real time and automatically optimize the process, enabling a single mold to have a lifespan of over a million cycles, meeting the large-scale production requirements for precise plastic parts in fields such as automobiles, electronics, and medicine.